【好文推荐】马国光,王金阳,张涛|二氧化碳捕集耦合工艺设计与优化
时间:2024-09-19 09:09:27
来源:本站
点击:535次
二氧化碳捕集耦合工艺设计与优化
1. 西南石油大学 石油与天然气工程学院,四川 成都 610500;2. 中国石油塔里木油田公司,新疆 塔里木 841000
摘 要采用醇胺法工艺对高含碳天然气进行脱碳处理时,其能耗随着碳含量的增加而提高。为降低高含碳天然气的脱碳能耗,提出了一种醇胺法工艺(N-甲基二乙醇胺作吸收剂)与级间冷却、富液分流解吸、酸气再压缩热泵和蒸汽机械再压缩技术(MVR)热泵工艺耦合的二氧化碳(CO2)捕集耦合工艺流程(“耦合工艺”)。采用Aspen Hysys软件对影响耦合工艺节能效果的关键参数(级间物流冷却温度、贫液节流后压力、酸气再压缩压力和再生塔底重沸器温度)进行了分析,并通过响应面分析与遗传算法结合的方式对关键参数进行了优化。结果表明,优化后耦合工艺的级间物流冷却温度为58 ℃、贫液节流后压力为0.084 MPa、酸气再压缩压力为0.195 MPa、再生塔底重沸器温度为92 ℃。与联合工艺(膜分离+醇胺法)相比,耦合工艺的能耗明显降低,脱碳单位能耗(脱除1 t CO2需要消耗的能量)由1.338 GJ/t下降至1.110 GJ/t。与优化前相比,耦合工艺优化后的净化气中CO2含量(体积分数)由2.533%下降至2.326%。脱碳单位能耗由1.110 GJ/t下降至1.074 GJ/t。
关键词CO2捕集;耦合工艺;参数优化;响应面法;遗传算法
为实现双碳目标,减少碳排放,油气企业需对高含碳天然气进行回收利用[1]。对于此类型天然气,国内目前一般采用膜分离+醇胺法联合脱碳工艺,但该工艺存在再生能耗较高和化学试剂损耗较大等缺点[2-3]。因此,开展针对二氧化碳捕集工艺节能措施的研究,对减少油气企业碳排放具有重要的现实意义。目前醇胺法是国内天然气行业运用最广泛的脱碳方法之一[4],一般采用Aspen Hysys软件对其进行模拟。该软件采用事件驱动,可较好地反映各变量之间的关系。刘建明[5]采用Aspen Hysys软件对活化N-甲基二乙醇胺(MDEA)脱碳流程进行了模拟,并通过控制变量法研究了半贫液循环量、循环温度、抽出位置和进料位置对能耗的影响,最终得出了较优的操作参数。对于高含碳天然气,一般采用膜分离+醇胺法联合工艺(简称“联合工艺”)进行脱碳。孔祥森[6]采用Aspen Plus软件对长岭天然气净化站进行了建模分析,依据经济性和可靠性原则得出天然气中CO2含量(体积分数,下同)为30%~90%时,醇胺法脱碳工艺已不具有适用性,采用多级膜工艺、膜分离+醇胺法联合工艺或变压吸附工艺更加合理。对脱碳工艺进行改进,充分利用流程中的余压与余热是提高经济效益、降低脱碳能耗的主要方法。陆诗建等[7]针对胜利电厂的烟气CO2捕集工程,利用Aspen Hysys软件构建了分布式换热工艺+蒸汽机械再压缩技术(MVR)热泵工艺+级间冷却工艺耦合的乙醇胺(MEA)醇胺法脱碳工艺,与单独的MEA醇胺法脱碳工艺相比,可节能33.56%。工艺参数的优化对最终节能效果同样有重要影响。响应面分析法是一种对响应值受多个变量影响的问题进行优化分析的方法。AROONSRI等[8]分析了不同类型的醇胺溶液与对应溶液浓度,以及汽提塔高度等参数对脱碳成本的影响。作者使用响应面优化方法对上述参数进行了优化,确定了课获得最低成本的参数组合。遗传算法是一种模拟达尔文生物进化论的自然选择和遗传学机理对目标进行优化的方法。DEBASISH等[9]对Lekhwair天然气处理站的醇胺法脱碳装置进行了研究,通过Aspen Hysys软件建立了仿真模型,并利用遗传算法对贫液进吸收塔温度、富液进再生塔温度和胺液循环量等参数进行了优化。结合使用响应面分析法和遗传算法,可有效提高优化效率和精度。闫龙[10]总结了遗传算法和粒子群算法等多种算法的特点,分析了结合算法的优势,并以某天然气醇胺法脱碳装置能耗最低为目标,使用结合算法对工艺参数进行了优化。结果表明,优化后装置能耗下降了10.35%。醇胺法脱碳工艺在烟气脱碳中运用广泛,将醇胺法脱碳工艺与节能工艺进行耦合可获得更好的节能效果。然而在高含碳天然气脱碳方面,多种工艺的耦合设计研究与应用较少,因此本文针对一种二氧化碳捕集耦合工艺进行研究,通过Aspen Hysys软件进行模拟,并运用响应面分析法与遗传算法相结合的方式对二氧化碳捕集系统进行优化,以期降低高含碳天然气脱碳能耗,提高二氧化碳捕集率,进而为高含碳天然气脱碳系统的节能改造提供参考。1二氧化碳捕集耦合工艺设计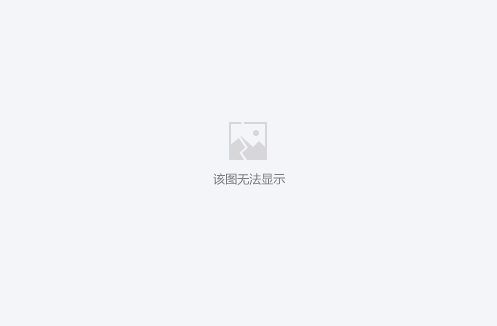
本研究中的研究对象为某油田产出的高含碳天然气,天然气处理量为17.2 × 104 m3/d(标况),温度为40 ℃,压力为2.2 MPa,原料气的组分和相应含量见表1。▼ 表1 原料气组成▼ Table 1 Compositions of feed gas

净化气中CO2含量按照GB17820—2018执行,即外输天然气中CO2最大合格含量不能超过4%。按体积售卖天然气时,CO2含量越高经济性越好,同时净化气中CO2含量越低所需的脱碳能耗越高。净化气中CO2含量的上限取4%,下限取2%。国内多采用醇胺法进行天然气脱碳,但由于原料气中CO2含量接近50%,常规醇胺法脱碳流程并不适用,且经过前期模拟分析和文献调研发现,联合工艺较其他工艺(如半贫液工艺)在此气质条件下具有更好的经济性和CO2捕集性能[11]。原料气在进入醇胺法脱碳流程前先经过膜分离过程进行粗脱,从而降低脱碳能耗,减少醇胺溶液用量。联合工艺流程见图1,该工艺的关键参数见表2。

▲ 图1 联合工艺流程▲ Fig. 1 Combined process flow▼ 表2 联合工艺的关键参数▼ Table 2 Key parameters of combined process

由图1和表2可知,联合工艺的能耗主要集中在胺液再生过程,并且系统内的余压与余热并未被充分回收与利用。在CO2吸收单元中,醇氨溶液吸收CO2是一个放热反应,而热量的积累不利于反应的正向进行,这导致醇氨溶液升温后的循环量比正常反应温度下的循环量大,其再生能耗也相应提高。在醇氨溶液再生单元中,再生塔塔顶气热能未被加以利用,这不但造成了塔顶气热能的浪费,还增加了再生塔顶冷凝器的能耗。在醇氨溶液再生单元中,再生塔底富液的热能未被充分利用,这导致再生塔底重沸器能耗较高且增大了贫液冷却器的负荷。因此,通过工艺耦合充分利用脱碳系统内的余压与余热是本研究的重点。针对上述问题,本研究拟通过传统工艺与级间冷却、富液分流解吸、酸气再压缩热泵和MVR热泵等工艺的耦合(简称“耦合工艺”,耦合工艺流程见图2),实现对系统内的余压与余热的充分利用。

▲ 图2 耦合工艺流程▲ Fig. 2 Coupled process flow为解决吸收塔反应放热不利于反应正向进行的问题,本设计采用了级间冷却工艺[12],将吸收塔第11块塔板处的溶液抽出,经冷却后再注入吸收塔内。该工艺改变了塔内的温度分布,促进了反应的正向进行,减少了醇胺溶液的循环量,从而降低了再生能耗。为解决再生塔冷凝器负荷高的问题,本设计采用了富液分流解吸工艺与酸气再压缩热泵工艺[13],将富液在进入贫液、富液换热器之前进行分流,一股物流进入再生塔顶部作为冷富液与压缩后的酸气进行换热,另一股物流正常进入再生塔。该工艺可对塔顶气的余热进行有效回收,不但减少了重沸器能耗,还降低了冷凝器负荷。为解决重沸器能耗高的问题,本设计采用了MVR热泵工艺[14],对再生塔塔底流出的贫液进行了节流降压,先将部分酸气闪蒸出来,然后对这部分酸气进行增压重新注入再生塔内。该工艺主要利用了酸气进入再生塔后与富液接触释放的大量热能,实现了对酸气余热的回收利用,有效降低了重沸器能耗。使用Aspen Hysys软件对耦合工艺进行了建模分析,由于化学溶液中含有醇胺成分,醇胺法部分采用了Acid Gas-Chemical Sovents(AGCS)物性方程。而气体膜分离工艺不涉及醇胺溶液,为保证Aspen Hysys仿真模型的可靠性和准确性,气体膜分离工艺采用Peng-Robinson(PR)物性方程进行计算,耦合工艺模拟基础数据见表3。▼ 表3 耦合工艺模拟基础数据▼ Table 3 Basic data for coupled process simulation

由表3可知,净化气中CO2含量为2.264%,符合相关国家标准,脱碳单位能耗为1.110 GJ/t。按照表3中的设置,在保持其他条件不变的情况下,采用单因素法分别对影响耦合工艺节能效果的关键参数(级间物流冷却温度、贫液节流后压力、酸气再压缩压力和再生塔底重沸器温度)进行了研究,以确定其寻优区间。
▲ 图3 级间物流冷却温度对净化过程与能耗的影响▲ Fig. 3 Effect of inter-stage flow cooling temperature on purification process and energy consumption由图3可知,随着级间物流冷却温度从40 ℃上升至58 ℃,富液酸气负荷略微下降(1%左右),净化气中CO2含量上升较快,增加了23.38%,装置总能耗和脱碳单位能耗总体呈下降趋势,装置总能耗下降了2.44%,脱碳单位能耗下降了1.88%。对于级间物流冷却温度来说,由于采用水循环制冷,本设计取循环水的温度为35 ℃,而设计水冷器时一般制冷温度比回水温度高4~6 ℃,故寻优区间下限取40 ℃,贫液进塔温度为58 ℃,级间物流冷却温度不应高于贫液进塔温度,故寻优区间上限为58 ℃,最终确定级间物流冷却温度寻优区间为40~58 ℃。贫液节流后压力对净化过程与能耗的影响见图4。由图4可知,当贫液节流后压力由0.070 MPa增加至0.110 MPa,富液酸气负荷及净化气中CO2含量均呈上升趋势,装置总能耗及脱碳单位能耗变化不大。对于贫液节流后压力而言,当贫液节流后压力小于等于0.080 MPa时,其产生的闪蒸气在增压后温度高于130 ℃,当闪蒸气进入再生塔与醇胺溶液接触时会增大MDEA溶液发生降解的概率,故寻优区间下限取0.080 MPa,贫液出再生塔压力为0.120 MPa,为确保贫液有一定的节流压降,因此寻优区间上限取0.110 MPa,最终确定贫液节流后压力的寻优区间为0.080~0.110 MPa。

酸气再压缩压力变化对净化过程与能耗的影响见图5。由图5可知,酸气再压缩压力变化对富液酸气负荷和净化气中CO2含量基本没有影响。随着酸气再压缩压力由0.120 MPa上升至0.210 MPa,再生塔底重沸器能耗、装置总能耗和脱碳单位能耗在0.200 MPa前均呈现下降趋势,并均在0.200 MPa时达到最低值,随后出现回升情况。对于酸气再压缩压力而言,压力大于0.200 MPa后,装置能耗出现回升情况,故取寻优区间上限为0.200 MPa,酸气出再生塔压力为0.110 MPa,为确保有一定的增压空间,故取寻优区间下限为0.120 MPa,最终确定酸气再压缩压力的寻优区间为0.120~0.200 MPa。

▲ 图5 酸气再压缩压力对净化过程与能耗的影响▲ Fig. 5 Effect of acid gas recompression pressure on purification process and energy consumption再生塔底重沸器温度对净化过程与能耗的影响见图6。由图6可知,随着再生塔底重沸器温度上升,富液酸气负荷及净化气中CO2含量总体上均呈均匀下降趋势,而装置总能耗及脱碳单位能耗总体上均呈均匀上升趋势。对于再生塔底重沸器温度而言,为使净化气中CO2含量低于联合工艺的相应值(2.533%),寻优区间下限取92 ℃,为确保净化气中CO2含量大于2%,寻优区间上限取94 ℃,最终确定再生塔底重沸器温度的寻优区间为92~94 ℃。

▲ 图6 再生塔底重沸器温度对净化过程与能耗的影响▲ Fig. 6 Effect of regenerator bottom reboiler temperature on purification process and energy consumption综合以上分析,为使产品质量达到国家标准,装置各关键参数的寻优区间见表4。▼ 表4 关键参数的寻优区间▼ Table 4 Optimization intervals of key parameters

为使耦合工艺达到最优运行状态,需对其运行参数进行优化。为解决Aspen Hysys软件优化器迭代速率慢、易出现不收敛等问题,本研究运用了响应面法与遗传算法相结合的方式进行参数寻优,其中响应面法用于建立输入变量和输出变量之间的关系模型,遗传算法用于寻找最优解。本研究以CO2捕集装置的节能为目的,因此以脱碳单位能耗最低为优化目标。对装置操作参数的优化是根据实际条件来调整决策变量,因此选择前文分析的关键工艺参数和净化气中CO2含量为决策变量。

式中,Y1为脱碳单位能耗,GJ/t;Ei为第i个装置的能耗,kW;p为压力,MPa;t为温度,℃;m为约束条件;Y2为净化气中CO2含量,%。需注意的是,式(1)中的约束条件是以装置各关键参数的寻优区间(表4)为约束条件,而净化气中CO2含量由响应面分析确定其定义式,其上限为2.533%,下限为2.000%。本研究中响应面实验自变量依次为级间物流冷却温度(Z1,℃)、贫液节流后压力(Z2,MPa)、酸气再压缩压力(Z3,MPa)和再生塔底重沸器温度(Z4,℃)。自变量的低、中和高水平分别以-1、0和1表示,响应值分别为Y1和Y2。采用Box-behnken design (BBD)响应面实验方案进行分析,结果见表5。
▼ 表5 响应面实验结果▼ Table 5 Results of response surface experiment



将式(2)作为遗传算法中的目标函数,式(3)和其中自变量作为约束函数的定义方程,遗传算法参数见表6。▼ 表6 遗传算法参数▼ Table 6 Genetic algorithm parameters

遗传算法是利用计算机仿真运算将问题的求解过程转换成类似生物进化中染色体基因交叉、变异的过程,本研究运用MATLAB软件进行优化。在表6的参数设置下,在第2代时子代种群间的平均适应度值和最佳适应度值已非常接近,在第9代时种群间个体差异很小,在经过13次迭代后收敛,耦合工艺的4个关键参数的优化结果见图7。

▲ 图7 最佳子代值▲ Fig. 7 Optimal subpopulation values为验证参数优化效果,将优化后的耦合工艺运行参数运用到仿真模型中,经过Aspen Hysys软件模拟得出了相应结果(表7)。▼ 表7 不同工艺运行参数对比▼ Table 7 Comparison of operational parameters of different process

由表7可知,耦合工艺优化后的脱碳单位能耗为1.074 GJ/t,与联合工艺的对应值(1.338 GJ/t)相比,降低了19.73%。同时净化气中CO2含量为2.326%,与联合工艺的对应值(2.533%)相比,降低了8.17%。本文设计了一套CO2捕集耦合工艺,并采用响应面分析法与遗传算法相结合的方式对耦合工艺进行了优化,得出如下结论。(1)优化后耦合工艺的级间物流冷却温度为58 ℃、贫液节流后压力为0.084 MPa、酸气再压缩压力为0.195 MPa、再生塔底重沸器温度为92 ℃。(2)与联合工艺相比,耦合工艺的脱碳单位能耗由1.338 GJ/t下降至1.110 GJ/t。与优化前相比,耦合工艺优化后的净化气中CO2含量由2.533%下降至2.326%,脱碳单位能耗由1.110 GJ/t下降至1.074 GJ/t。